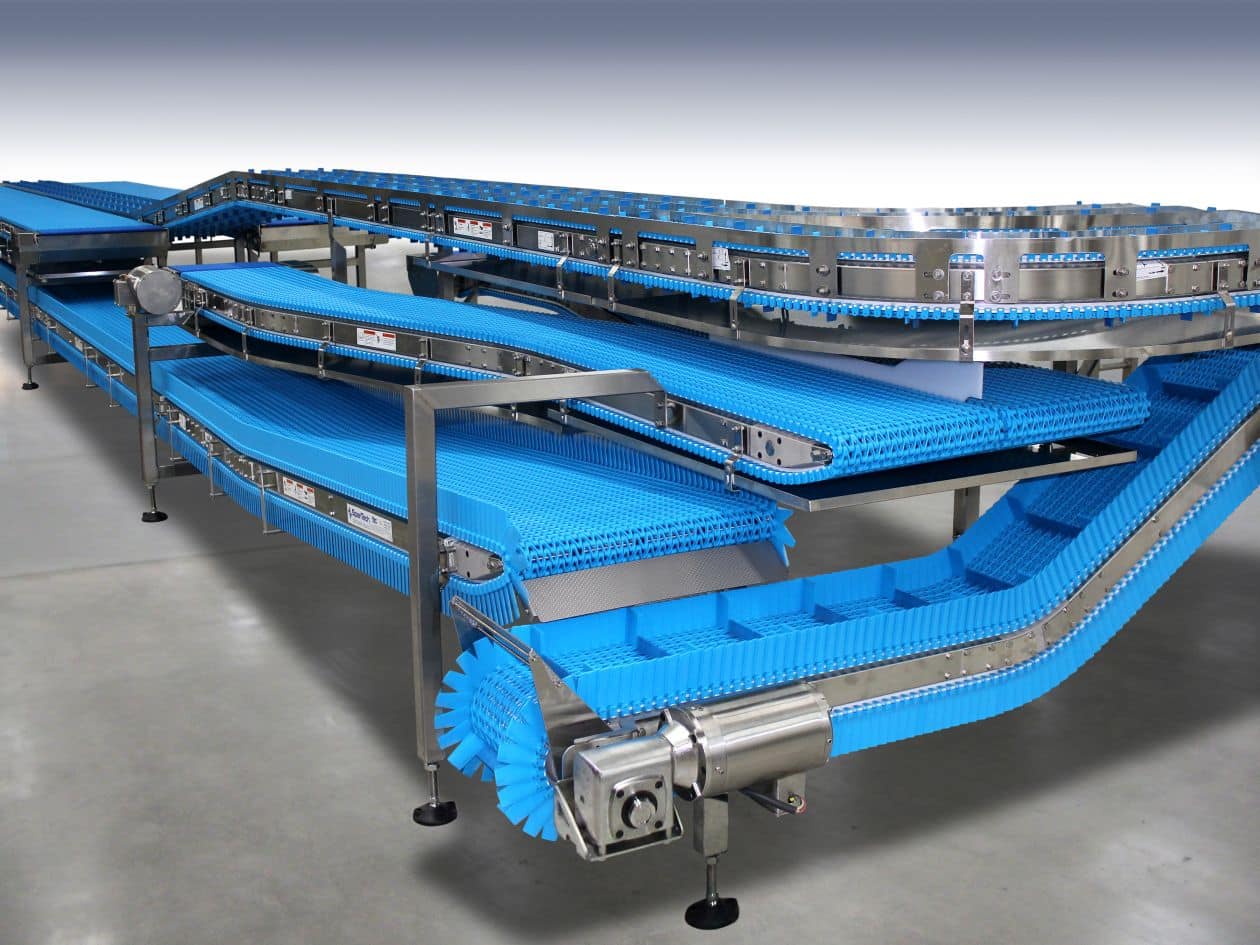
Material Handling Conveyors: Types, Uses & Optimizations
All Products
How can we help you?
Contact us at the Consulting WP office nearest to you or submit a business inquiry online.
3 Main Types of Conveyors Used in Material Handling
1. Transportation Conveyors
Transportation conveyor systems move pallets, cartons, or other material handling products from point A to point B. They can be used for a variety of applications from heavy full-pallet loads to lightweight items that vary in size. Transportation conveyor options are available to accommodate requirements such as desired speed and product handling procedures.
There are three main types of transportation conveyors: gravity conveyors, belt conveyors and live roller conveyors.
- Gravity conveyors are made up of a frame, rollers or wheels and are pitched so gravity can move product or allow product to be moved manually down the line. Gravity conveyors are ideal for applications such as assembly lines, where products need to be smoothly transitioned from one station to the next without the need for powered assistance, or for shipping areas to expedite the movement of packages from the packing area to the delivery truck.
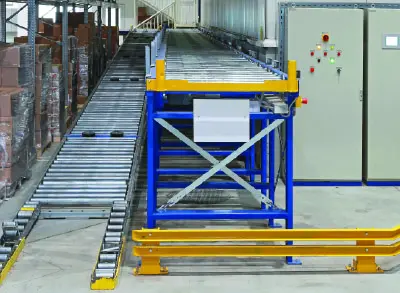
- Belt conveyors, one of the most commonly used material handling conveyor types, uses pulleys and a wide belt that are supported by rollers or a flat pan along its path to move product. Belt conveyors are commonly utilized in the food industry for the transportation of packaged goods or raw materials from one processing area to another, as their flat and smooth surface makes them easy to clean and maintain.

- Roller conveyors push loads by applying power to either some or all the rollers. Live roller conveyors are perfect for heavy or irregularly shaped objects that require additional support and control during transportation, such as in the automotive industry where components of varying sizes need to be moved along the assembly line.
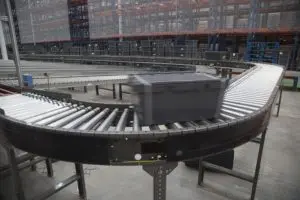
2. Accumulation Conveyors
Accumulation conveyor systems simultaneously move loads from point A to point B, while allowing them to accumulate when necessary to allow time for equipment or other material handling resources to become available.
Once these resources become available, the system gives a signal to release the next queue of products. There are three main types of accumulation conveyors: zero pressure accumulation conveyors, zero contact accumulation conveyors and minimum contact accumulation conveyors.
- Zero pressure accumulation conveyors allow for light contact between products when the system signals that queue to accumulate. Zero pressure accumulation conveyors are well-suited for applications involving fragile or sensitive products, such as electronics or glass items, as they minimize the chance of damage by allowing for light contact between items when queued to accumulate.
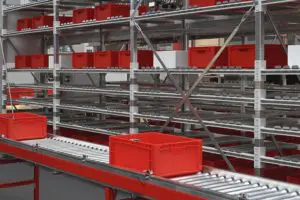
- Zero contact accumulation conveyors leave space between products when the system signals a queue to accumulate. Zero contact accumulation conveyors are ideal for situations where product spacing is crucial, such as in the food and beverage industry where contamination needs to be prevented, or for products with irregular shapes that may get entangled if they come in contact with each other.
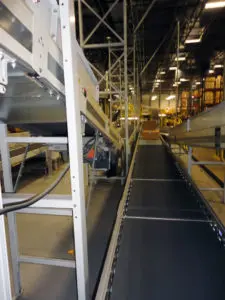
- Minimum contact accumulation conveyors maintain a light but constant drive force on products waiting to accumulate. Minimum contact accumulation conveyors are useful in scenarios where products need to be kept in a specific orientation or alignment while waiting in a queue, such as in the packaging industry where items need to be in the correct position for labeling or sealing.
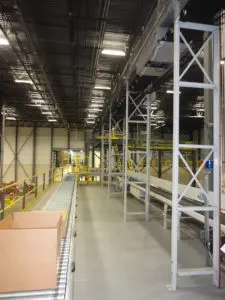
3. Sortation Conveyors
Sortation conveyor systems are used to direct products from one conveyor line to another. These conveyors integrate an induction system; system merges and sortation diverts. These are tailored to each operation to properly identify, track and transport products to expedite the order fulfillment process. These conveyors are best suited for high throughput operations that require products to flow to numerous locations.
There are seven types of sortation conveyors: shoe sorters, pop-up wheel sorters, right angle transfers, arm/pusher sorters, narrow belt sorter, tilt tray sorter and cross-belt sorter.
- A shoe sorter conveyor system supports produce on tubes or slates and a “shoe” positively diverts product to either side. Shoe sorters are ideal for sorting a wide range of product sizes and weights, shoe sorters are commonly used in retail distribution centers to organize products for specific stores or regions.
- Pop-up-wheel sorter conveyor system utilizes a belt conveyor with added rows of angled wheels at divert areas. Pop up wheel sorters are suitable for medium-speed sorting of lightweight, small to medium-sized packages, and often used in e-commerce fulfillment centers to sort parcels to specific destinations.
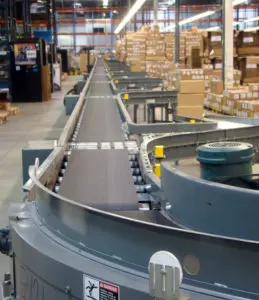
- Right angle conveyor system transfers utilize a transfer head to push the product off a conveyor onto a perpendicular or parallel conveyor. Perfect for operations where space is limited, right-angle transfers can move products onto perpendicular or parallel conveyors, making them ideal for intricate conveyor systems with multiple pathways.
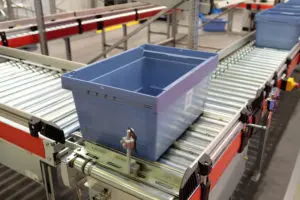
- Arm/pusher style sorter conveyor system divert products onto chutes that are 90-degrees from the sorting conveyor. A narrow belt sorter is designed with multiple narrow belts that transport the product. Commonly used in manufacturing facilities, arm/pusher sorters can divert products onto chutes at 90-degree angles, which is useful for organizing products based on different processing or packaging requirements.
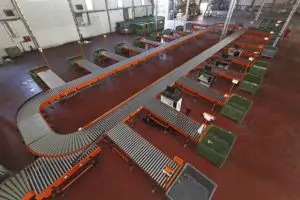
-
- Narrow belt sorter conveyor system consists of a series of narrow belts that span the width of the conveyor, each with its own take-up. At the point of sortation, the belts divert in unison to guide the product towards its designated location, either to the left or right of the conveyor. This type of sorter is effective for handling small to medium-sized products and is commonly used in industries such as retail, parcel handling, and e-commerce.
- Tilt tray sorter conveyor system uses a tilting tray at divert points to slide each item onto the proper chute. Lastly, the cross-belt sorter utilizes a series of small, individual belted trays which are activated when an item needs to divert off one conveyor onto another at a 90-degree angle. This versatile solution for sorting a wide range of product sizes and shapes is often used in retail and e-commerce distribution centers for sorting items to specific destinations or order fulfillment
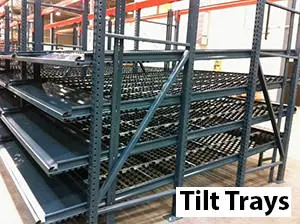
-
- Cross-belt sorter conveyor system is a high-speed conveyor system equipped with a series of small, individual belts (carriers) mounted on a chain that transports items to their designated locations. Each belt can move independently, allowing products to be sorted and discharged at 90-degree angles to either side of the conveyor, facilitating accurate and efficient sorting for a range of industries, such as e-commerce, logistics, and retail distribution. The system’s flexibility and precision make it a popular choice for facilities that handle a diverse range of product sizes and types.
- Cross-belt sorter conveyor system is a high-speed conveyor system equipped with a series of small, individual belts (carriers) mounted on a chain that transports items to their designated locations. Each belt can move independently, allowing products to be sorted and discharged at 90-degree angles to either side of the conveyor, facilitating accurate and efficient sorting for a range of industries, such as e-commerce, logistics, and retail distribution. The system’s flexibility and precision make it a popular choice for facilities that handle a diverse range of product sizes and types.
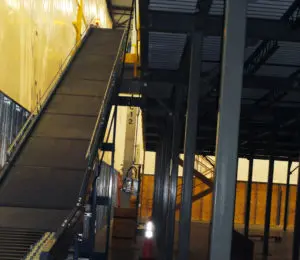
Benefits of Custom Material Handling Conveyors for Industrial Environments
Custom material handling conveyors are specifically designed to meet the unique requirements of different industrial settings, providing several key benefits:
Adaptability to Different Materials
Conveyors can be tailored to handle various types of materials, ensuring that they are transported safely and without damage. This is crucial in preserving the quality and integrity of products throughout the handling process.
Enhanced Efficiency and Productivity
By accommodating various production processes, conveyors optimize workflow and minimize downtime. This streamlined operation significantly enhances efficiency, which in turn boosts overall productivity.
Automation has significantly transformed material handling conveyors, propelling them to new heights of efficiency. Automated and semi-automated conveyors, outfitted with sophisticated sensors, controls, and artificial intelligence, provide precision in the movement and handling of materials, thereby minimizing human error and maximizing productivity. These smart systems are capable of real-time tracking and monitoring of goods, ensuring accurate delivery and effective inventory management, ultimately optimizing the entire supply chain process.
Scalability for Industry Changes
Conveyors are designed with scalability in mind, allowing for easy adjustments and modifications as the needs of the industry evolve. This flexibility is vital for businesses that anticipate growth or changes in their operations over time.
Integration with Existing Systems
Conveyors can be seamlessly integrated with existing material handling systems, ensuring a cohesive and efficient operation. This integration is essential for maintaining a smooth workflow and preventing bottlenecks in the production process.
Cost-Effectiveness
While the initial investment in a conveyor may be high, the long-term savings realized through improved efficiency, reduced product damage, and ada
Related Products
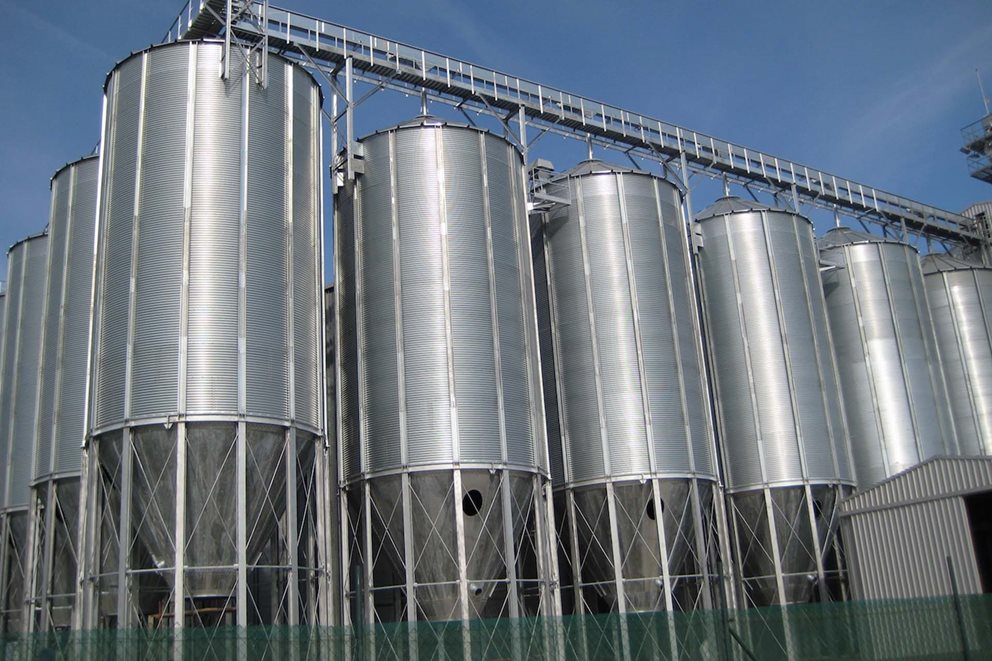
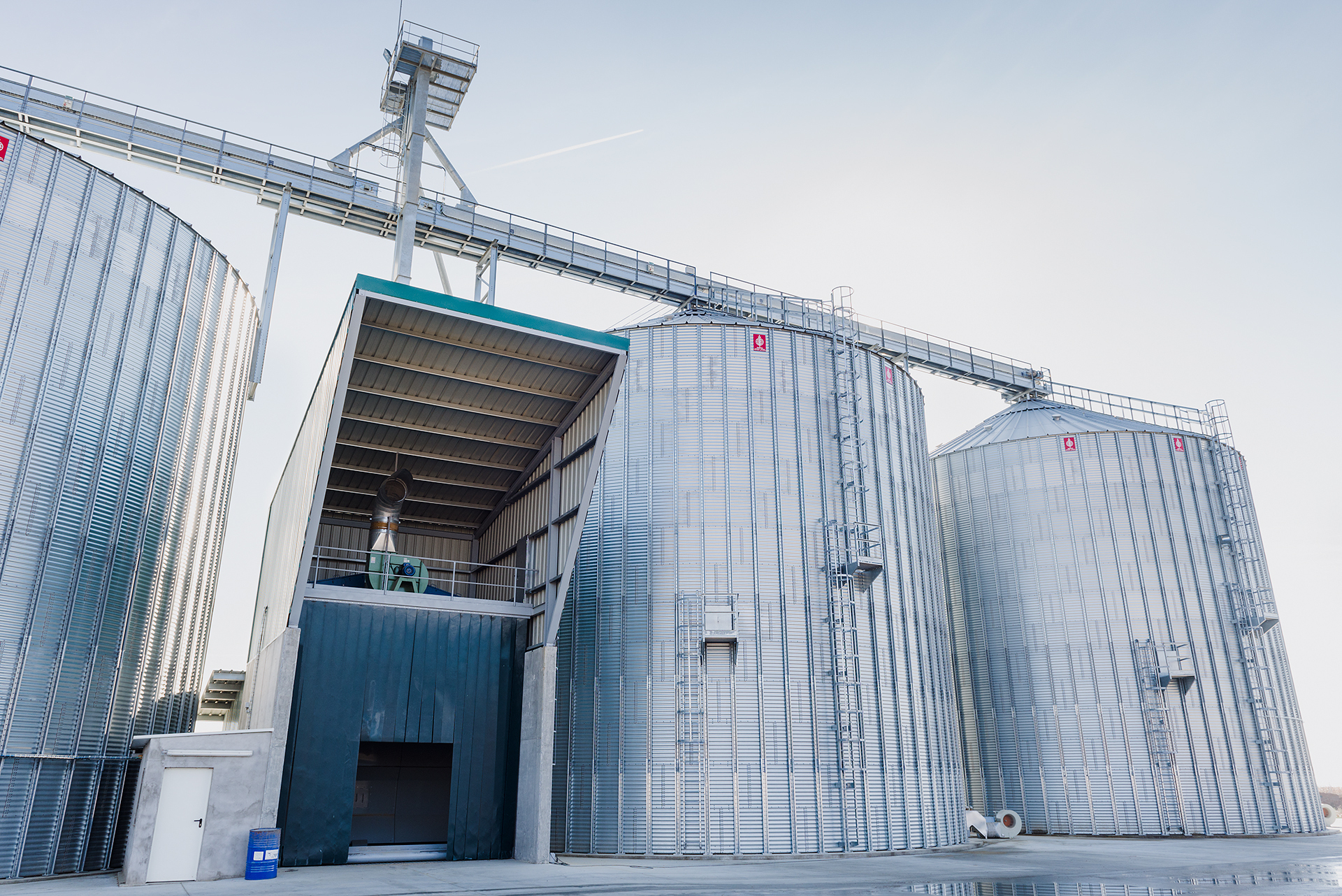
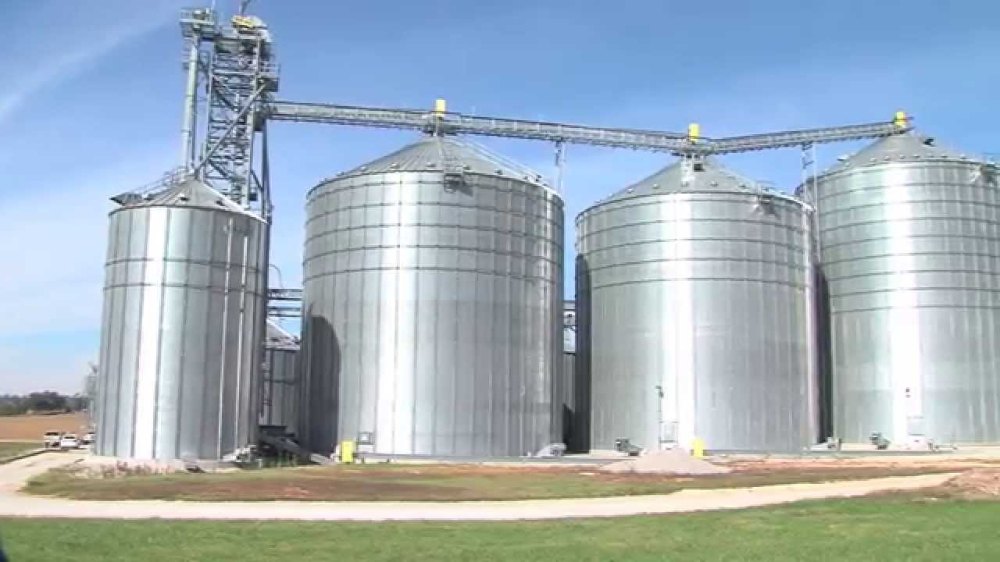
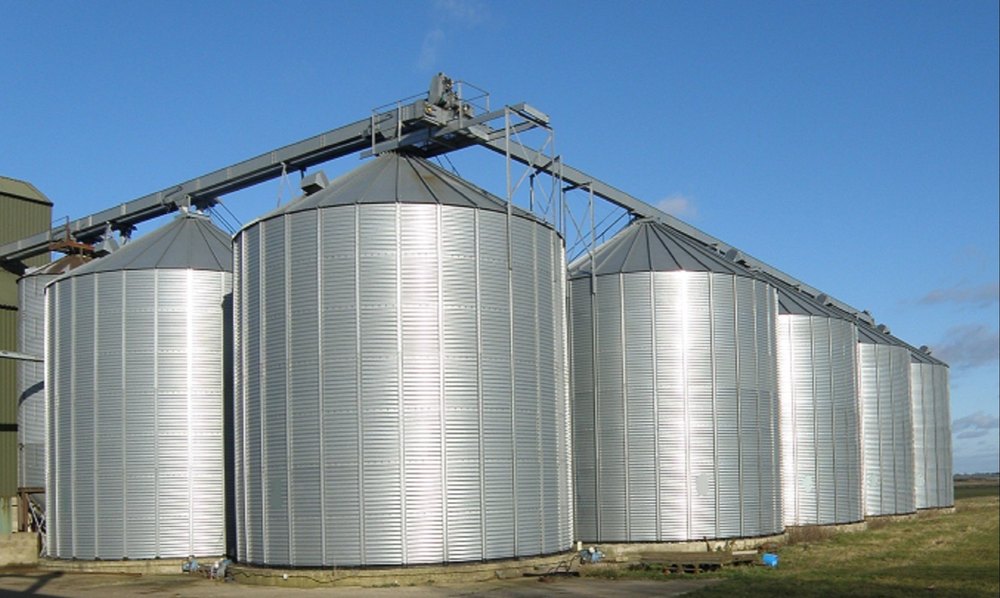
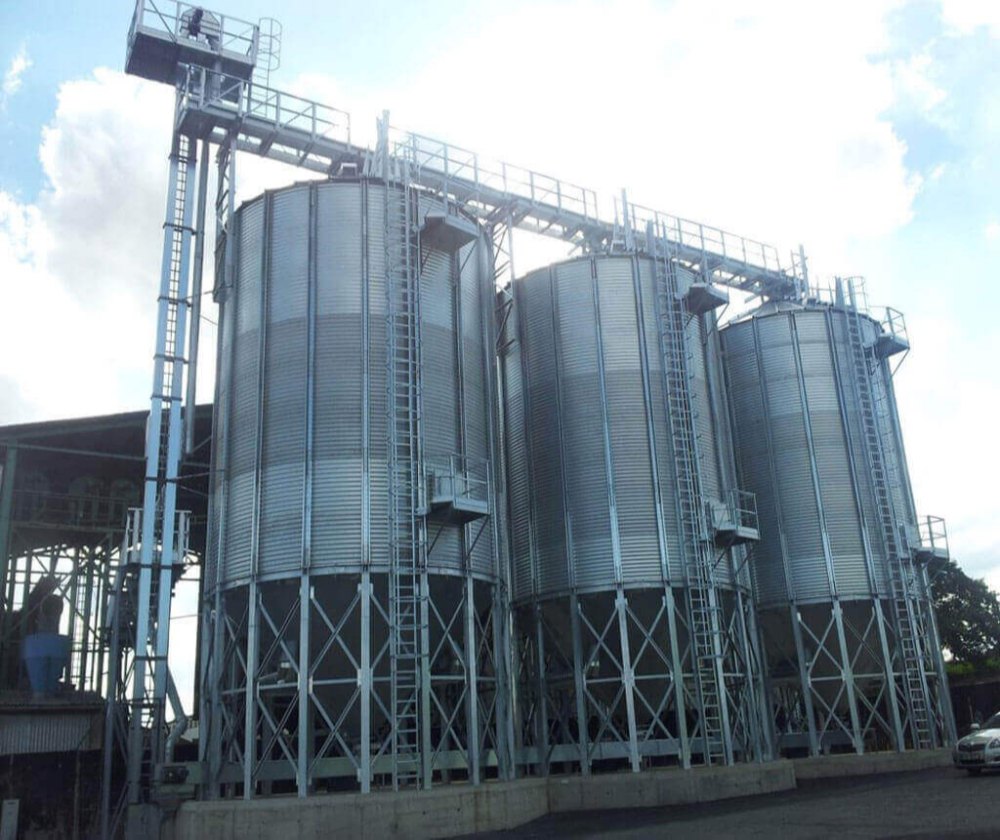
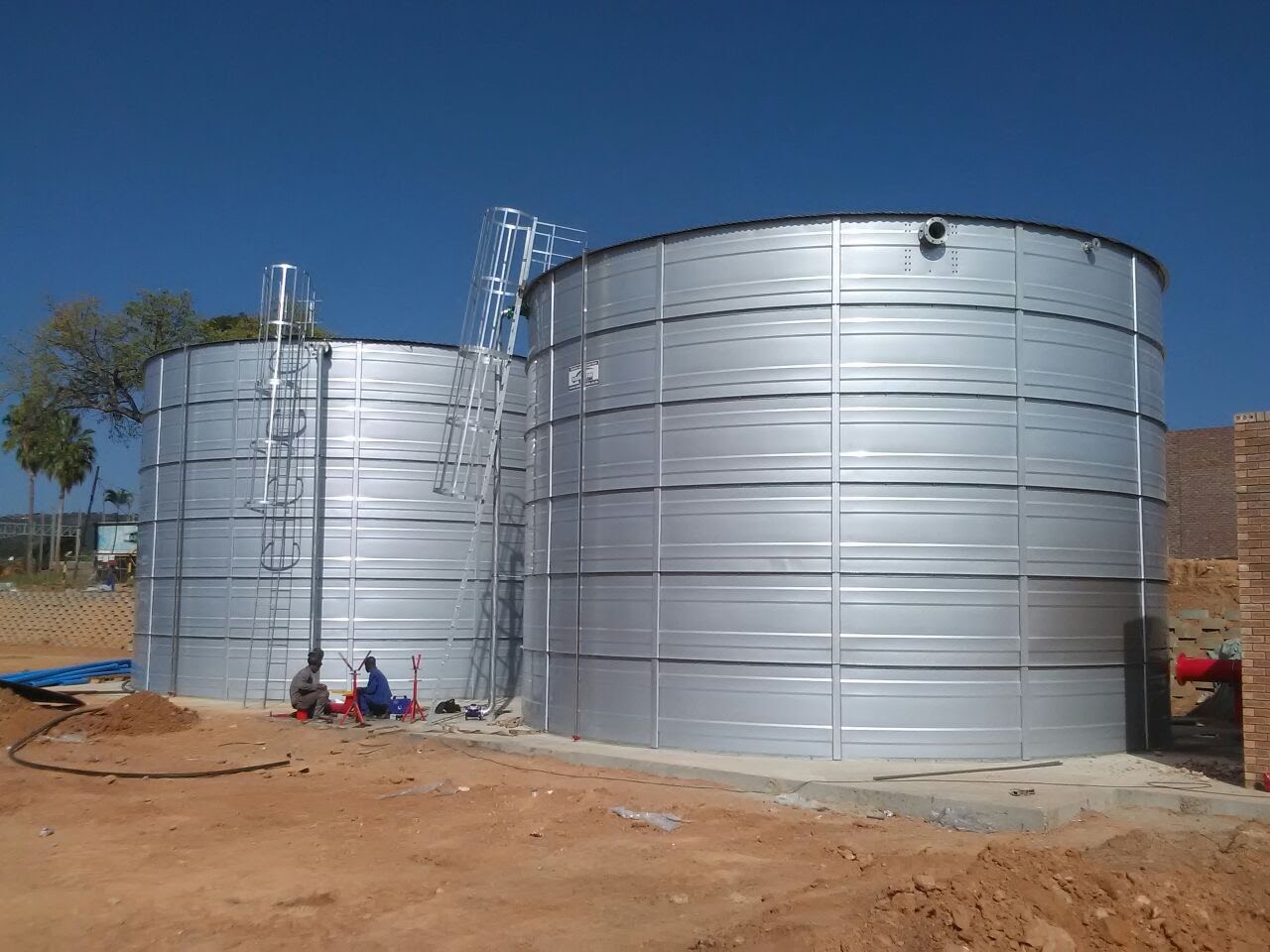
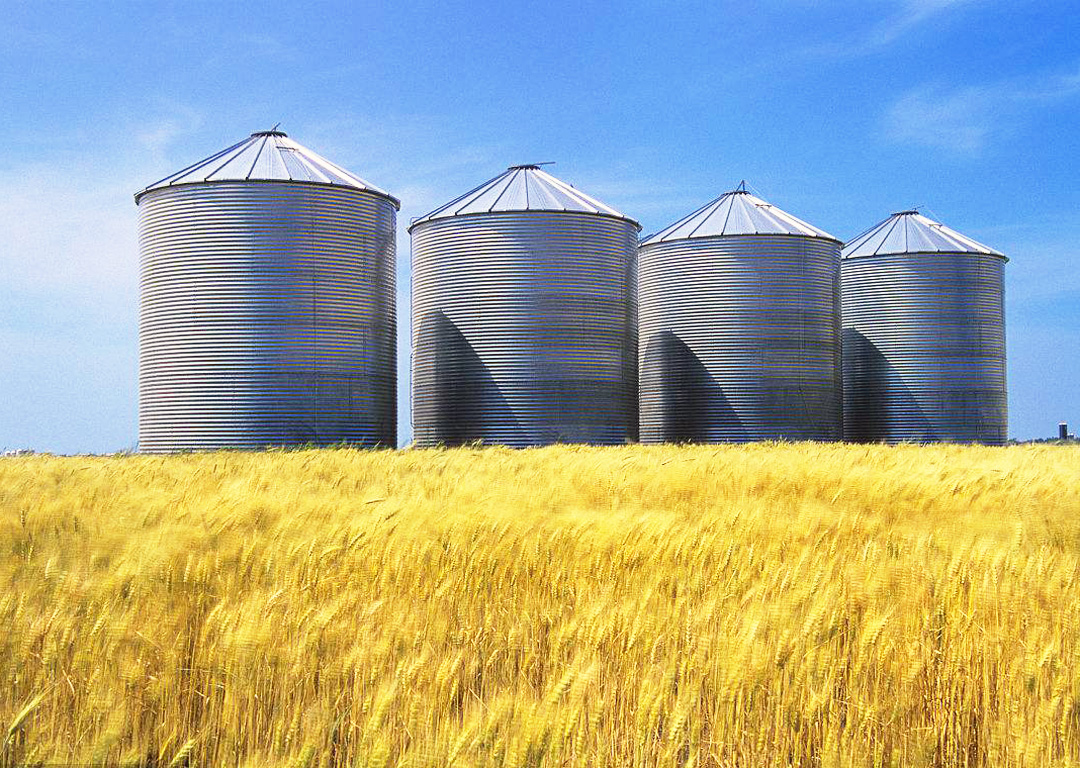
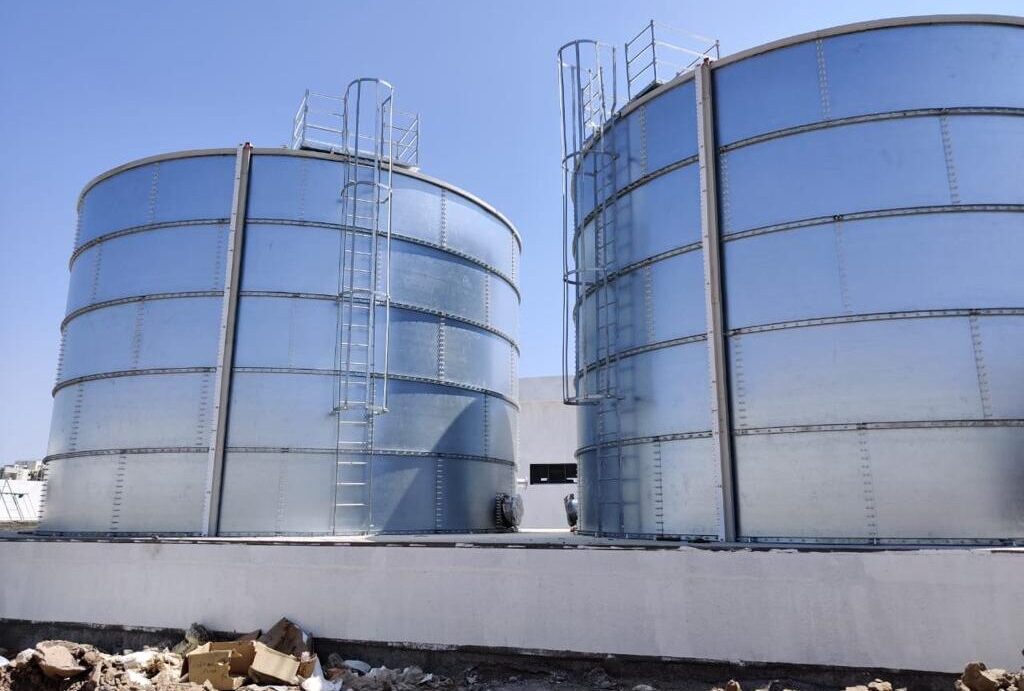
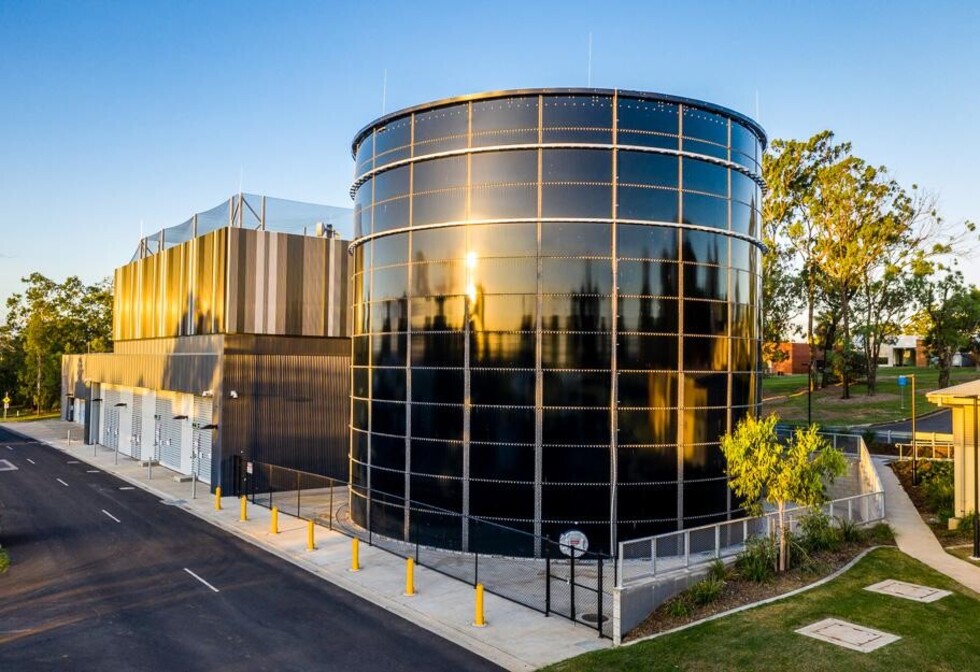
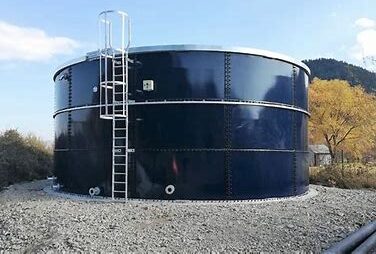
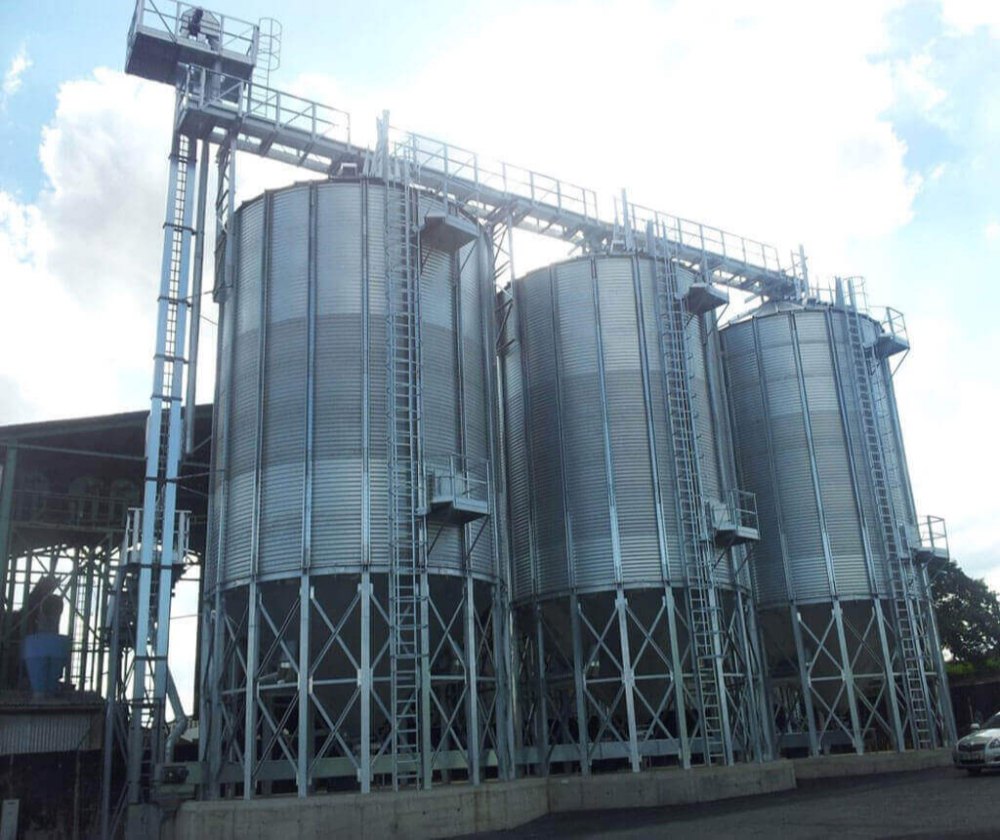