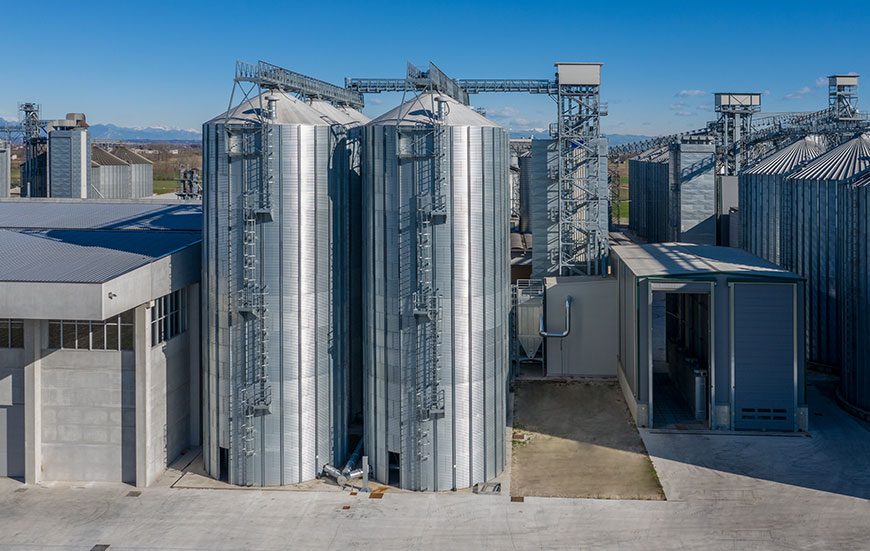
Introduction of hopper silo
All Products
How can we help you?
Contact us at the Consulting WP office nearest to you or submit a business inquiry online.
Innovation and advantages
- Simplified and more reliable static calculation.
- Easier foundation with slab.
- Use of crane or framework not needed.
- Assembly always from the ground.
- Availability of space under the silo.
- Electrical equipment installed in a closed space.
Unique details of hopper bottom silo
Fine Touch Steel has so many successful silo project in the world, what makes our customers choose Fine Touch Steel silos instead of other silos. Here is a picture of Fine Touch Steel hopper bottom silo details.
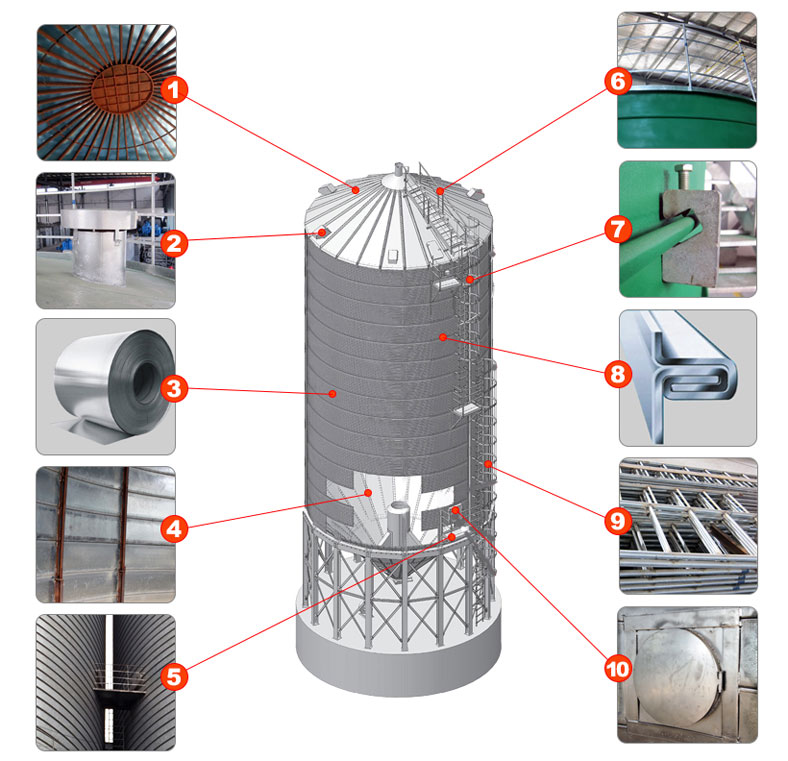
1. Silo Roof Inside
The silo roof is firmly fixed on the silo by welding, and the inside is strengthened by using many sniffier, the painted components inside the roof can prevent corrosion and do not afraid of heavy rains, heavy snows or other bad weather.
2. Roof Air Vent
When the air inside the silo expels from the silo, the air vent is activated, the air will be pushed out.
3. Silo Body Galvanized Coils
Our galvanized coils are with 275g/m2 zinc which is higher than the national standard to make sure the silo is anti corrosion and can serve for longer time.
4. Steel stiffener
The steel stiffener is used to strengthen the stability of the silo. With these stiffeners, the silo can stand still in strong wind and bad weather. The stiffener weld on the plate uses double weld panels to hold the stiffener.
5. Rest Platform
The rest platform is designed on for workers who check the silo condition and would have a small place during if get tired. It is much safe for works to have a rest during long time outside work.
6. Roof Ladder Handrail
This part is help to keep safe of workers, It provides convenience for workers’ operation and ensures their safety.
7. Silo Clamping Apparatus
It can keep the silo free from the impact of outside temperature, and can prevent the silo from splitting in the welding process.
8. Lipp Construction Technology
The Lipp double-seam technology is an advanced technology in the world which requires certain assembly equipment. The edge of the steel strips are folded twice which make both sheet bit tight and provide a great sealing effect.
9. Ladder System
The ladder is built outside of the silo for worker to to check to condition of the silo. The ladder is the access to the top of the silo.
10. Silo Gate
The silo gate is well sealed with double gate, inside one and out side one, which is safe and anti corrosion.
Details
- 30° conical shape.
- The roof panels are manufactured with S-350GD - Z 600 high tensile steel sheets or can be pre-painted galvanized steel sheet upon request.
- The static calculation is performed by the finite element method for:
- Each individual local wind, snow and seismic load.
- Additional heavy duty loads of the catwalks on the roof.
- Temperature probe loads.
- The roof is a self-supporting structure.
- Roof panels are assembled with galvanized steel bolts and plastic seal washers. Stainless steel bolts can be delivered upon request.
- The roof is equipped with:
- A) d = 500 mm or d = 600 mm inlet flange.
- B) Air vents allowing for the circulation of the existing air in the silos with the incoming grain.
- C) Inspection hatch, located at the silo eave which allows for:
- Visual control of the stored product.
- Taking samples.
- Maintenance of the maximum level indicator.
- This inspection hatch is equipped with a rest platform which can be reached either by a ladder fixed on the silo wall starting from ground level or by a drop down ladder from the catwalk fixed to a relevant post.
- The wall panels are manufactured with S-350GD - Z600 hot dip Sendzimir galvanized high tensile steel sheets which can be painted upon request.
- The static calculation is performed using an in-house developed software for each individual grain density as well as any local wind, snow and seismic loads.
- Wall sheet:
- A) Shape is 104 mm corrugation which reduces friction and product residues.
- B) Assembly by 2 or 3 rows of bolts according to the thickness and acting loads.
- Vertical stiffener:
- A) Standard omega section and junction.
- B) Reinforced wide omega section and junction.
- Wind rings, if necessary, according to the static calculation.
- 45° or 60º with d = 400 mm standard outlet flange and from 750 mm to 1400 mm outlet height.
- STANDARD SOLUTION (“with skirt”), consisting of:
- A) Self-supporting inner hopper (for diameters up to 5.30 meters).
- B) Inner hopper with support structure for diameters from 6.10 to 12.20 meters.
- C) Inner hopper and support structure manufactured with S-350GD steel, hidden by the silo wall itself.
- D) Extended cylindrical wall of the silo itself, reinforced with double stiffeners.
- E) Quick assembly, without crane.
- Hopper silos are equipped with a flanged access door located in the hopper which can be reached by a short mobile ladder or directly from the ground level.
- Roof panels are assembled with galvanized steel bolts and plastic seal washers. Stainless steel bolts can be delivered upon request.
- Wall sheets are assembled by high tensile steel 8.8 or 10.9 quality hot dip galvanized bolts with double steel and plastic seal washers.
- Wall sheets are assembled by 2 or 3 rows of bolts, according to the thickness and acting loads.
Downloads
Related Products
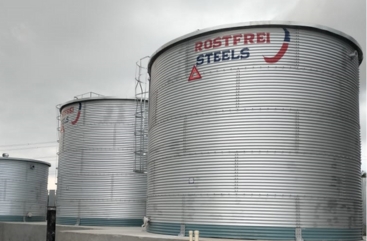
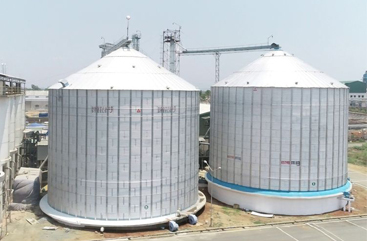
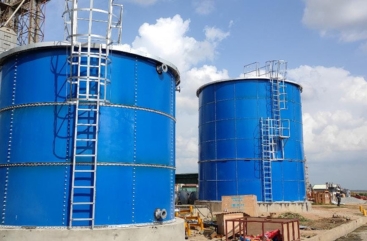
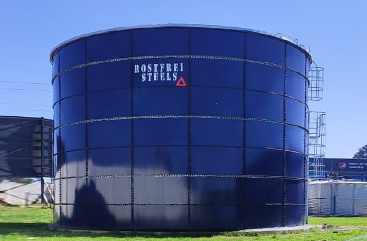
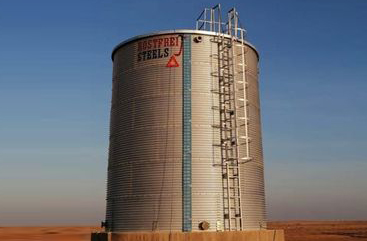