Flat Bottom Silos
Flat Bottom Silos
Flat Bottom Silos
Previous slide
Next slide
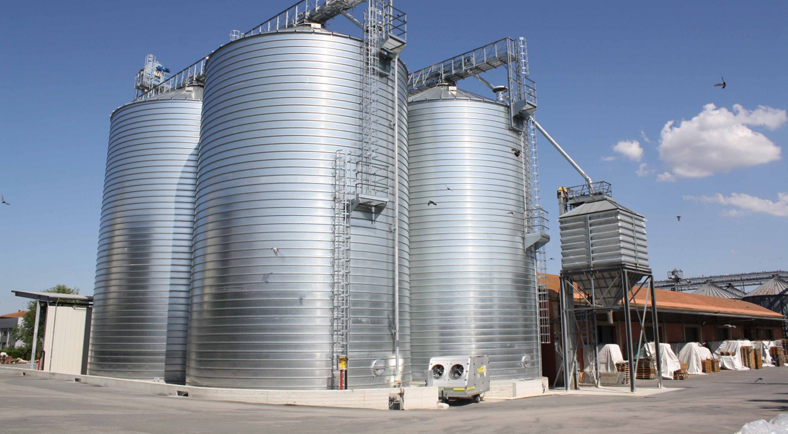
Flat Bottom Silos: From 50MT to 15000MT on Wheat
With a heartbreaking figure of 10% of total foodgrain yield getting wasted in India due to inadequate storage infrastructure, it’s high time that we reconsider using conventional storage methods like gunny bags, concrete structures and MS storage structures. The wastage is mainly caused due to moisture affecting the grainsand extreme temperature variation resulting infungus formation and minimal handling of food grains.
Fine Touch offers the ideal solution with world-class Galvanized Silo Storage Systems - the best and safest storage & grain handling systems with grain management that provide a new-age answer for the same age-old problems. The Silos are engineered using the best materials and proven technology for optimum temperature and humidity control. They retain the quality of stored grains for a longer duration while reducing wastage as well as manpower costs. Fine Touch Provides Single Window end to end Complete Project Management right from collecting requirement from customers, Design, Engineering, Manufacturing, Erection and Commissioning & Life cycle support.
Fine Touch offers the ideal solution with world-class Galvanized Silo Storage Systems - the best and safest storage & grain handling systems with grain management that provide a new-age answer for the same age-old problems. The Silos are engineered using the best materials and proven technology for optimum temperature and humidity control. They retain the quality of stored grains for a longer duration while reducing wastage as well as manpower costs. Fine Touch Provides Single Window end to end Complete Project Management right from collecting requirement from customers, Design, Engineering, Manufacturing, Erection and Commissioning & Life cycle support.
All Products
How can we help you?
Contact us at the Consulting WP office nearest to you or submit a business inquiry online.
Our Flat Bottom Silos deliver versatility by involving simple assembly techniques resulting in minimal installation costs and highly efficient low cost storage. They offer a capacity range of 50-15,000 tonnes. For larger diameters, a galvanized reinforced roof structure is incorporated considering various loadings of overhead conveyor and wind. Also, internal reinforcement rings are installed to prevent deformation due to winds.
Benefits of Silo System
- Scientific method of storage i.e. bulk storage
- No wastage of gunny bags due to bulk grain storage
- Requires less space app (1/4) compared to godown storage of same capacity
- Mechanized handling with automation requires no manpower hence handling cost is less
- No spillage, no wastage due to rodents, insects, birds etc.
- Quality of the stored grain maintained by aeration system along with temperature monitoring device
- Compatible for fumigation - Optional
Features
- 8.8 quality dichromate bolts and nuts are used
- Neoprene washers to ensure waterproof seal
- All silo components are galvanized regardless of thickness that provide excellent anti-corrosion qualities
- Hot dip galvanized legs support structure with ring beam
- Capable of storing any flowable commodity such as grains, seeds, feed, plastic pellets and certain material supplements
- Galvanized cross section roof structure on models with a diameter higher than 12.22 meters
Details
- 30° conical shape.
- The roof panels are manufactured with S-350GD - Z600 high tensile steel sheets or can be pre-painted galvanized steel sheet upon request.
- The static calculation is performed by the finite element method for:
- Each individual local wind, snow and seismic loads.
- Additional heavy duty loads of the catwalks on the roof.
- Temperature probe loads.
- The roof is a self-supporting structure up to 10 m in diameter. Beyond this diameter the roof is equipped with an independent supporting structure.
- Roof panels are assembled with galvanized steel bolts and plastic seal washers. Stainless steel bolts can be delivered upon request.
- The roof is equipped with:
- A) d = 500 mm, d = 600 mm or d= 900 mm inlet flange according to the capacity of the conveyor system.
- B) Air vents allowing for the circulation of the existing air in the silos with the incoming grain.
- C) Inspection hatch, located at the silo eave which allows for:
- Visual control of the stored product.
- Taking samples.
- Maintenance of the maximum level indicator.
- This inspection hatch is equipped with a rest platform which can be reached either by a ladder fixed on the silo wall starting from ground level or by a drop down ladder from the catwalk fixed to a relevant post.
- The wall panels are manufactured with S-350GD - Z600 hot dip Sendzimir galvanized high tensile steel sheets which can be painted upon request.
- The static calculation is performed using an in-house developed software for each individual grain density as well as any local wind, snow and seismic loads.
- Wall sheet:
- A) Shape is 104 mm corrugation and depth 12 mm in wall sheet which reduces friction and product residues.
- B) Assembly by 2 to 4 rows of bolts according to the thickness and acting loads.
- Vertical stiffener:
- A) Standard omega section and junction.
- B) Reinforced wide omega section and junction.
- Anchorage:
- A) Base plate with double anchor bolts, mechanical or chemical type.
- B) Spacer plates in order to compensate tolerance of the foundation (optional).
- Flat Bottom Silos are equipped with a hinged double type lateral access door with a hot dipped galvanized steel frame in the second ring of the wall.
- This door is designed according to a safety concept which only allows for opening if the upper level of the stored product is below the door.
- This door allows for:
- A) Easy entrance to the silos.
- B) Final cleaning of the bottom and aeration floor or channels.
- C) Control and maintenance of the sweep auger.
- Additional lateral access doors can be installed above the angle of repose to suit customer needs.
- Roof panels are assembled with galvanized steel bolts and plastic seal washers. Stainless steel bolts can be delivered upon request.
- Wall sheets are assembled by high tensile steel 8.8 or 10.9 quality, hot dip galvanized bolts with double steel and plastic seal washers.
- Wall sheets are assembled by 2 to 4 rows of bolts, according to the thickness and acting loads.
- Base plates are anchored to the concrete foundation by M16, 20, 24 galvanized mechanical or chemical bolts, according to the statics.
Technical Specifications
Downloads
Related Products
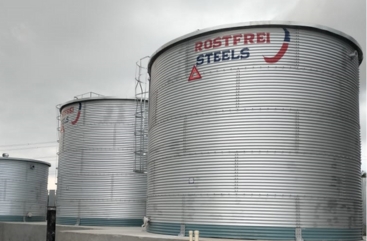
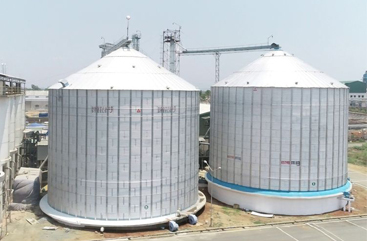
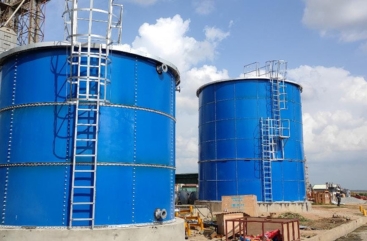
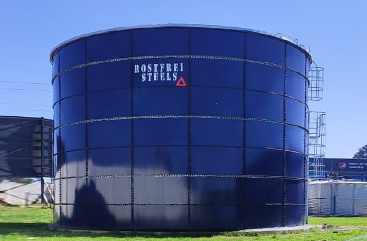
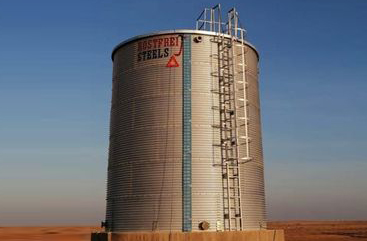