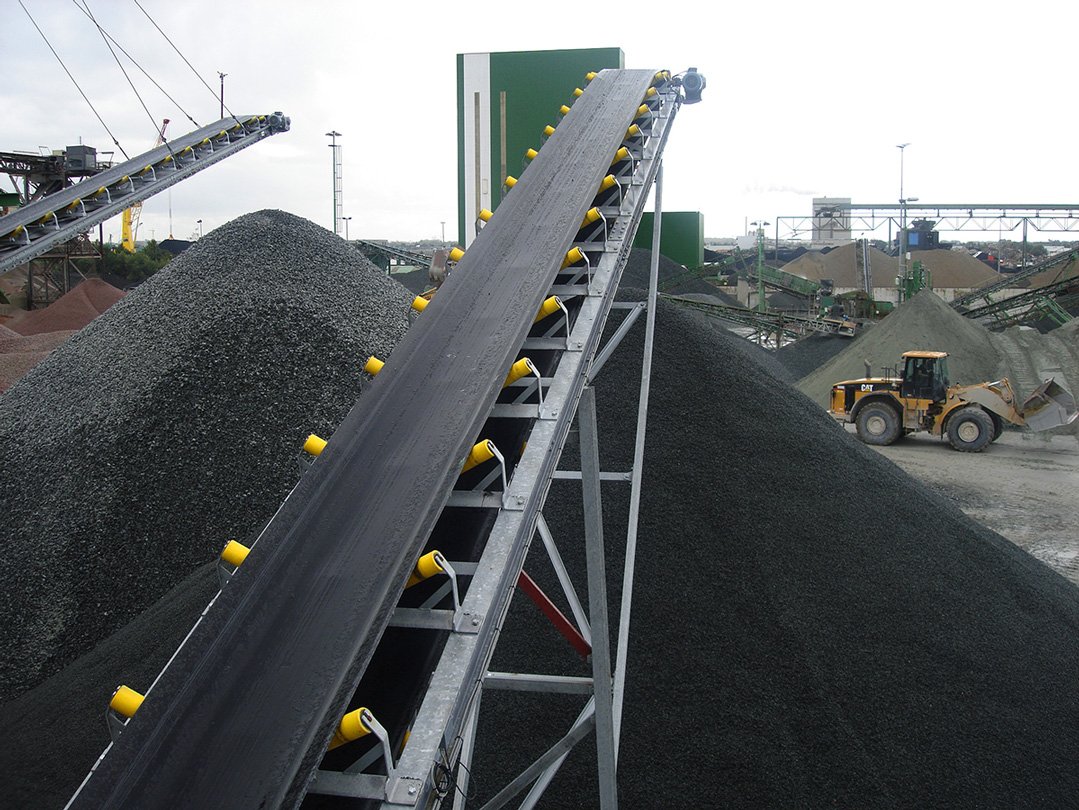
Belt Conveyors
This article will take an in-depth look at belt conveyors.
The article will bring more understanding on topics such as:
Belt Conveyors and their Components
Types of Belt Conveyors
Design and Selection of Belt Conveyors
Applications and Benefits of Belt Conveyors
And Much More…
All Products
How can we help you?
Contact us at the Consulting WP office nearest to you or submit a business inquiry online.
Chapter 1: Belt Conveyors and their Components
This chapter will discuss what a belt conveyor is and its components.
What is a Belt Conveyor?
A belt conveyor is a system designed to transport or move physical items like materials, goods, even people from one point to another. Unlike other conveying means that employ chains, spirals, hydraulics, etc., belt conveyors will move the items using a belt. It involves a loop of a flexible material stretched between rollers that are actuated by an electrical motor.
Because the items being transported vary in nature, the belt material also varies by the system it is employed in. It commonly comes as a polymer or a rubber belt.
Components of a Belt Conveyor
A standard belt conveyor system has a head pulley, tail pulley, idler rollers, belt, and frame.
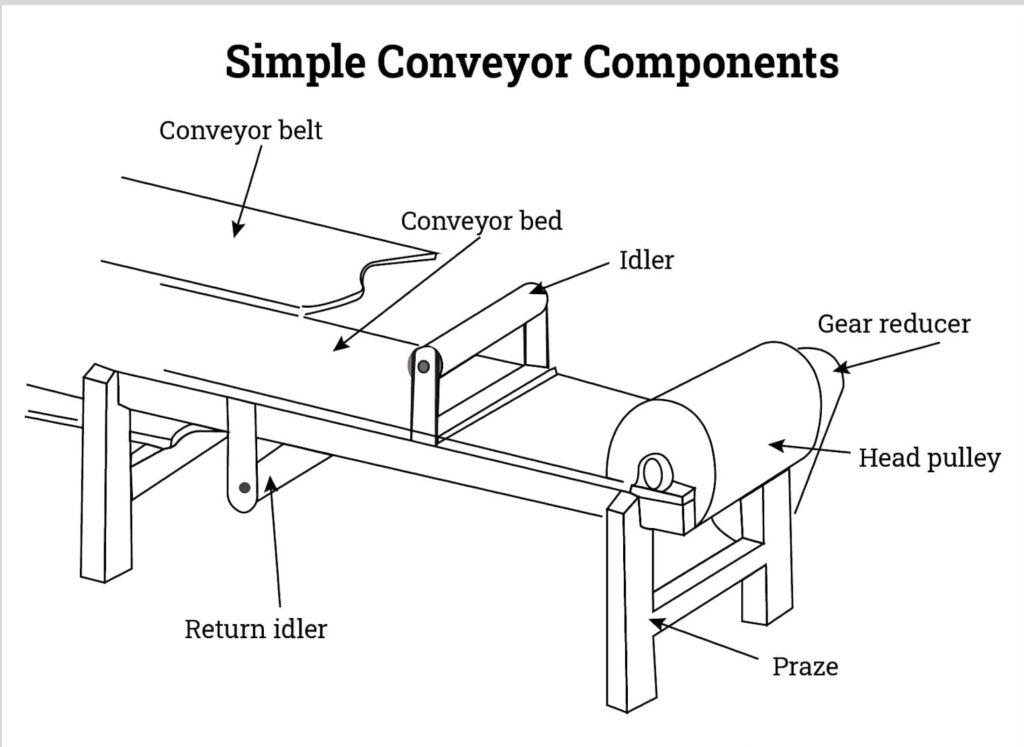
Head Pulley
The head pulley is coupled with the actuator and the electric motor. It drives the conveyor, acting as the pulling force. The head pulley is located at the point that the conveyor offloads, known as the discharge end of a belt conveyor. Since it drives the whole system, it is often necessary to increase the traction of its belt with a rough jacket covering its outer surface. The jacket is referred to as a legging.
The head pulley usually has the largest diameter of all the pulleys. Sometimes a system can have multiple pulleys that act as drive pulleys. The pulley at the discharge end, is a drive roller usually with the biggest diameter, and will be identified as the head pulley.
Return or Tail Pulley
This is located at the loading end of the belt conveyor. Sometimes it comes with a wing shape to clean the belt by letting material fall aside to the support members.
In a simple belt conveyor setup, the tail pulley will be mounted on guides usually slotted to allow the belt’s tension. In other belt conveying systems as we shall see, tensioning of the belt is left to another roller called the take-up roller.
Idler Roller
These are rollers employed along the length of the belt to support the belt and load, prevent sagging, align the belt, and clean up the carryback (material left sticking on to the belt).
Idler rollers can either do all of the above or any one of them, but in any space, they will always act as support for the belt.
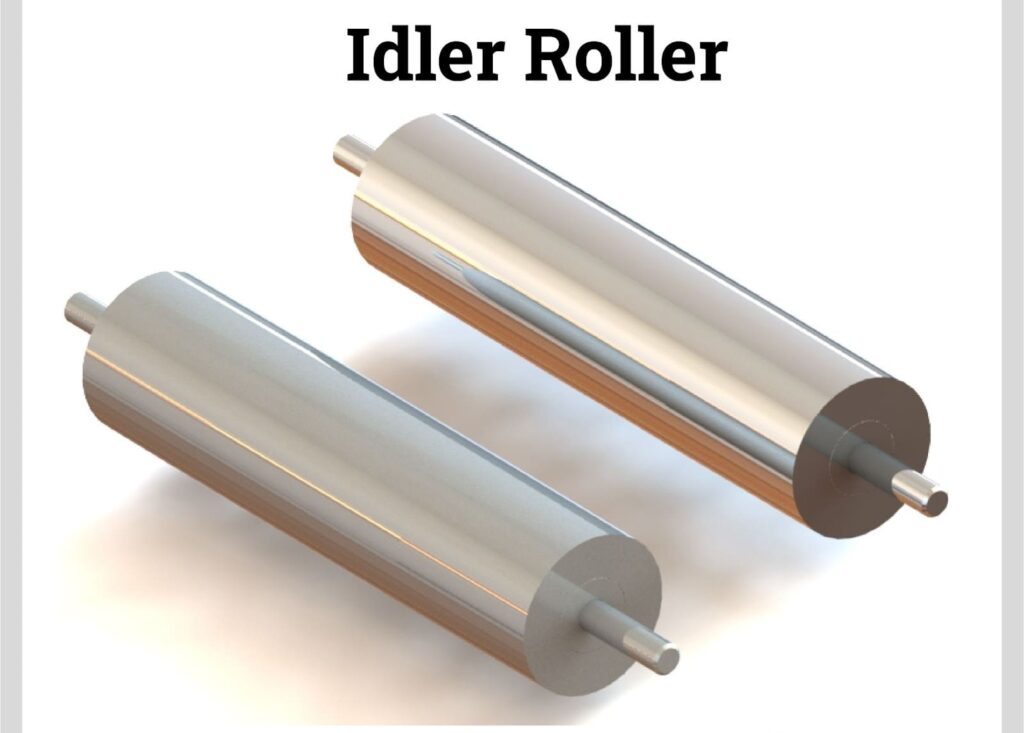
There are many different idler rollers for different functions, as listed below:
Troughing Idlers
Troughing idlers will have three idler rollers set up in a configuration that makes a “trough” of the belt. They are located on the side that carries the load on the belt conveyor. The idler in the center is fixed, with the two on the ends able to be adjusted. This is so the angle and depth of the trough can be varied.
These idlers, when employed, will reduce spillages and maintain a constant cross-sectional area along the length of the belt conveyor. Maintaining a constant cross-sectional area is important for stability.
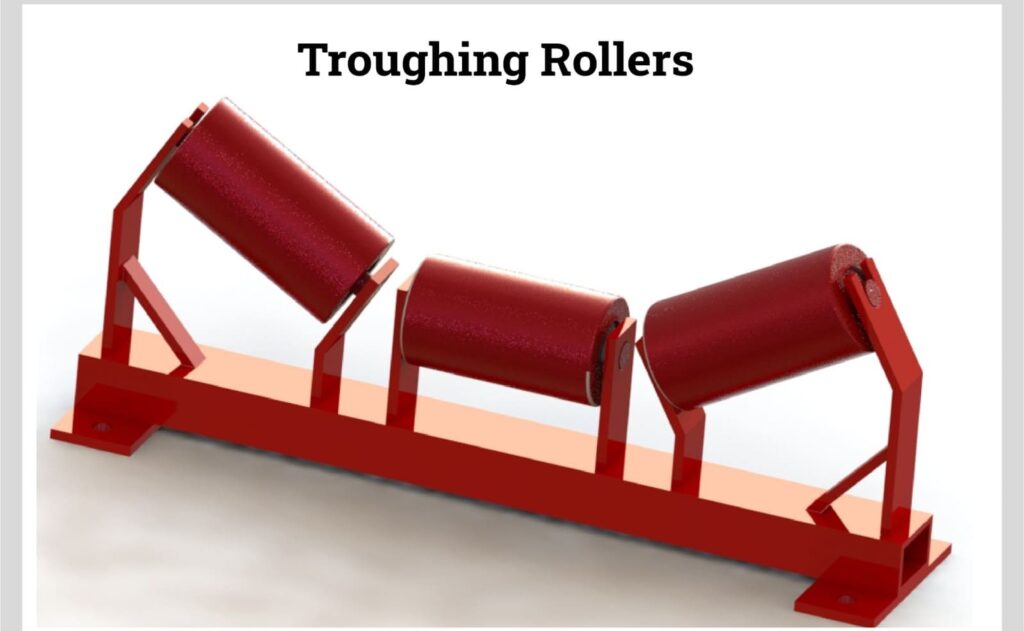
Rubber Disk Idler
This idler has rubber disks placed at set distances along the axis of the roller. On the extreme ends, the rollers are much closer so that they can support the belt edge, which is prone to tear. The spaced-out disks will break off any connected carryback/ leftover material and reduce material building up on the bottom of the belt. This is a common cause for mistracking (when the belt shifts to one side of the system and causes misalignment).
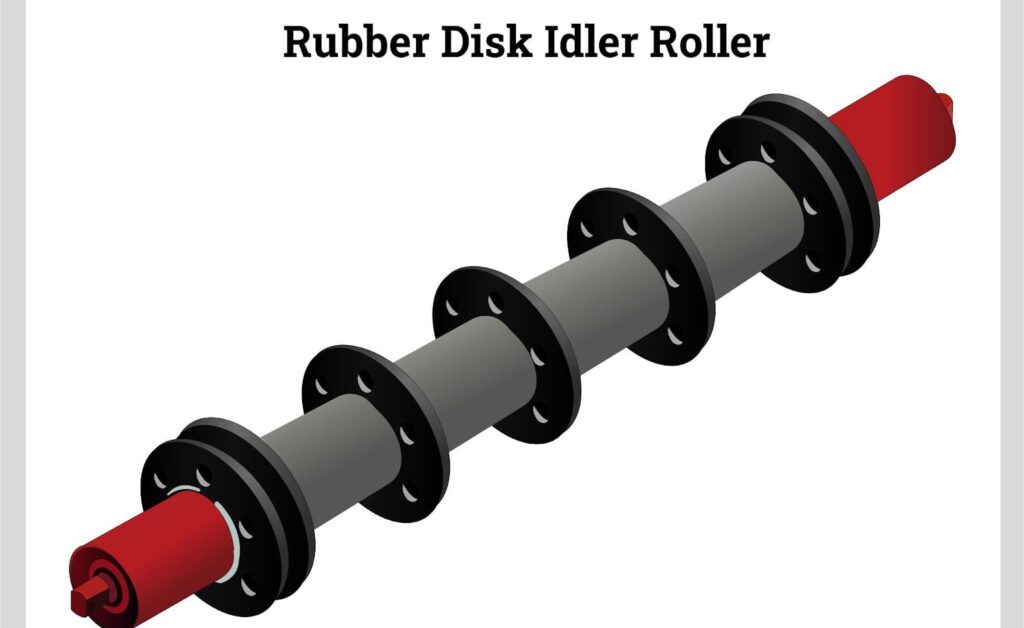
Screw Idler Roller
Sometimes the disks are helical like a screw and the idler will be called a rubber screw idler roller. The function will remain the same. An example of a screw idler roller is depicted below.
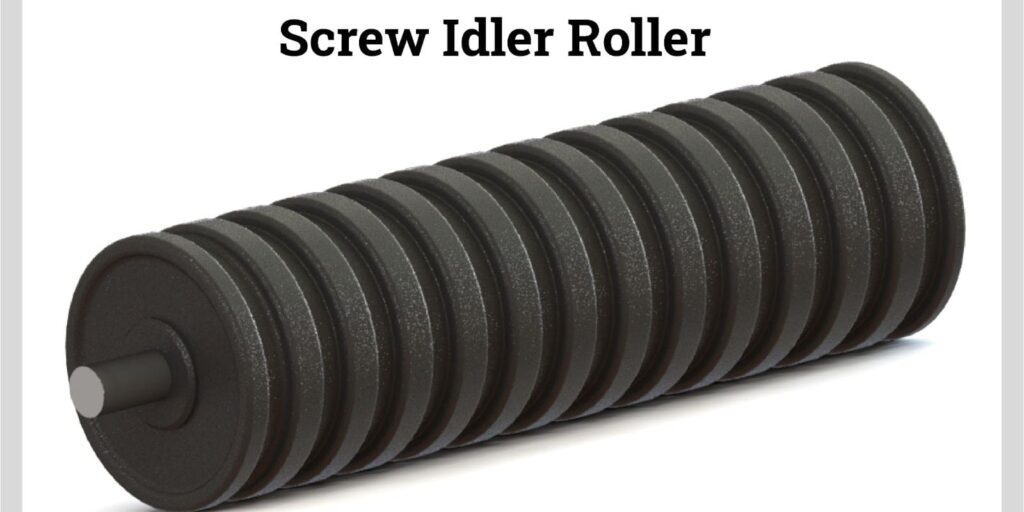
The screw idler can also be made out of rubber helix. Screw idlers are most common where a scrapper that takes off carryback would not be feasible, especially on mobile belt conveyors.
Trainer Idler
Trainer idlers keep the belt running straight. It works against mistracking. It achieves this by a central pivot that swerves the roller back to the center should the belt drift off to one side. It also incorporates two guide rollers to act as guides for the belt.
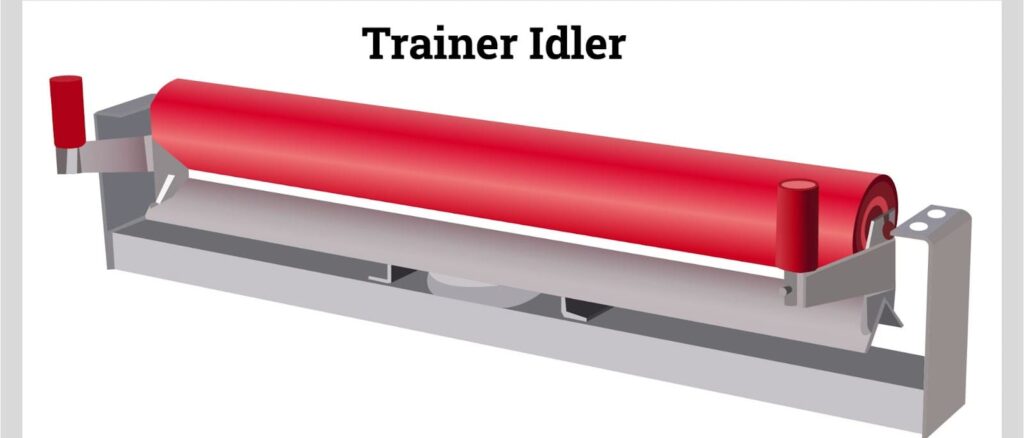
Conveyor Belt
In setting up a belt conveyor, the belt is perhaps the most intricate.The tension and strength are important since the belt takes a lot of punishment when loading and ferrying the material.
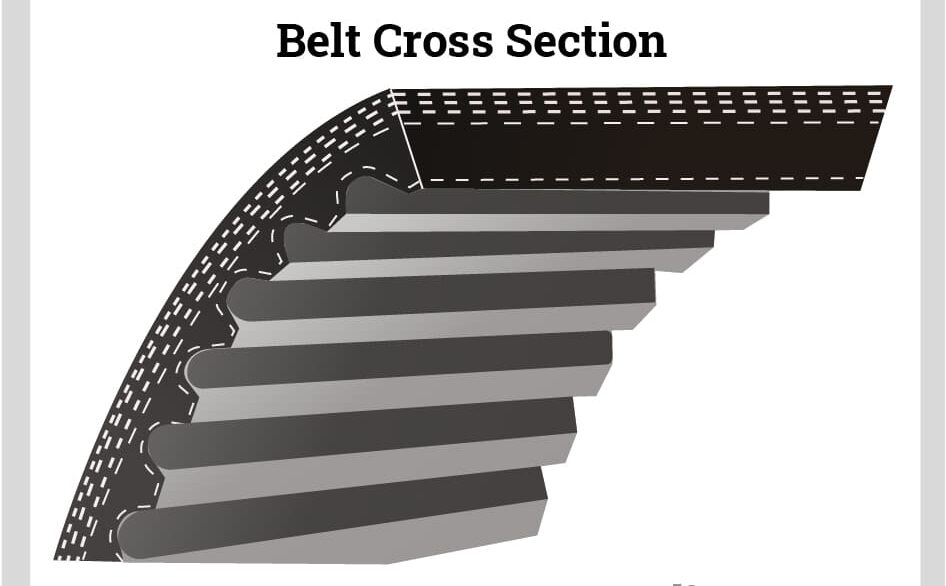
The growing demand for longer conveying lengths has catalyzed the research into new materials, though this always comes at a cost. Stronger belts that adhere strictly to environmentally friendly rules tend to come with high setup costs, sometimes the costs can hardly even be justifiable. On the other hand, if an economical approach is taken, the belt usually fails, resulting in high operating costs. Costs for the belt should usually range below 50% of the total cost for the belt conveyor.
A belt is made up of components such as:
Conveyor Carcass
Since this is the skeleton of the belt, it has to provide the tensile strength needed to move the belt and the lateral stiffness for supporting the load. It must also be capable of absorbing loading impact. The belt is a loop so it has to be joined; this is known as splicing. Because some of the splicing methods require the use of bolts and fasteners, the carcass must be able to provide an adequate and firm base for these fasteners.
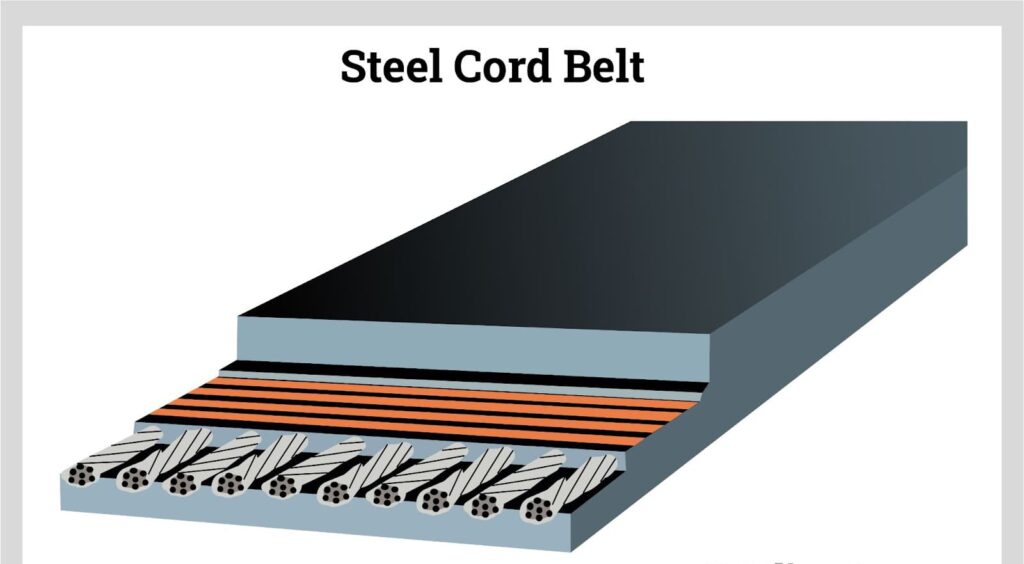
The carcass is commonly made of steel cord or textile ply. Textile ply is made from fibers like aramid, polyamide, and polyester. If only one ply is used, a PVC-coated textile carcass is also common. Carcasses can have even six layers piled on each other. The carcass can also include the edge protection that is very much needed in bulk conveyor belts.
Conveyor Covers (Top and Bottom & Sides)
This is a flexible material made of rubber or PVC. The covers get exposed directly to the weather elements and the working environment. Careful consideration of the covers must be made depending on the intended use. The following usually require attention, flame resistance, low-temperature resistance, grease and oil resistance, anti-static, and food grade.
The carrying side of the conveyor depending on the load, the angle of inclination of the conveyor, and general use of the belt all have special features. It can be corrugated, smooth, or cleated.
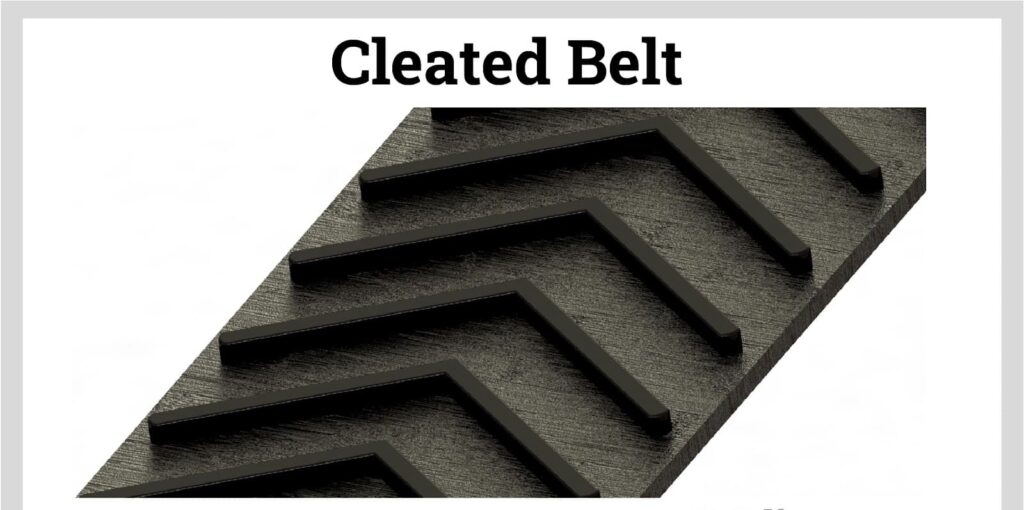
Related Products
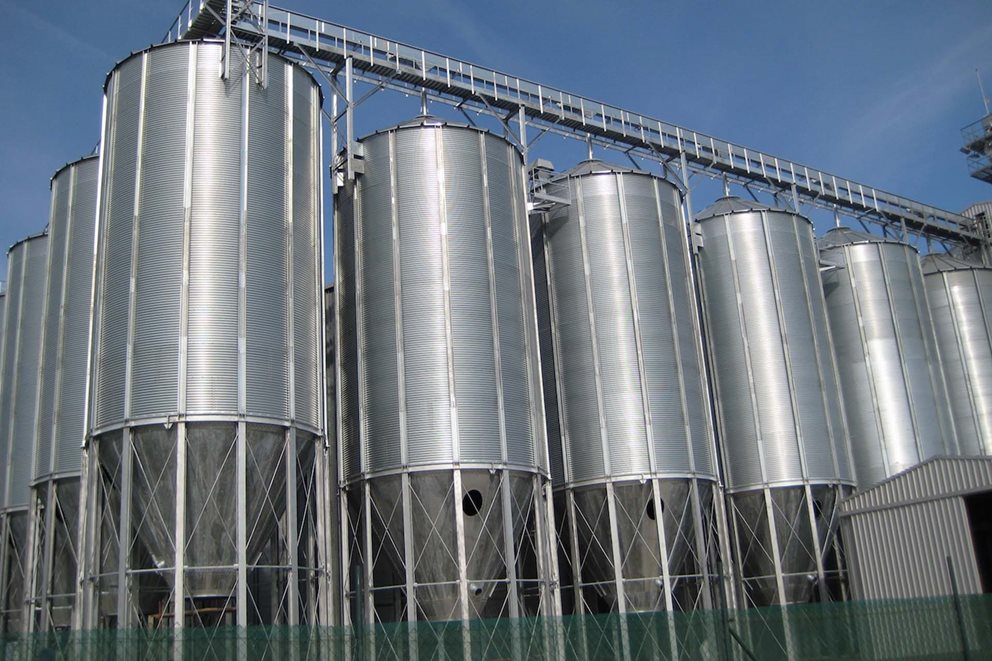
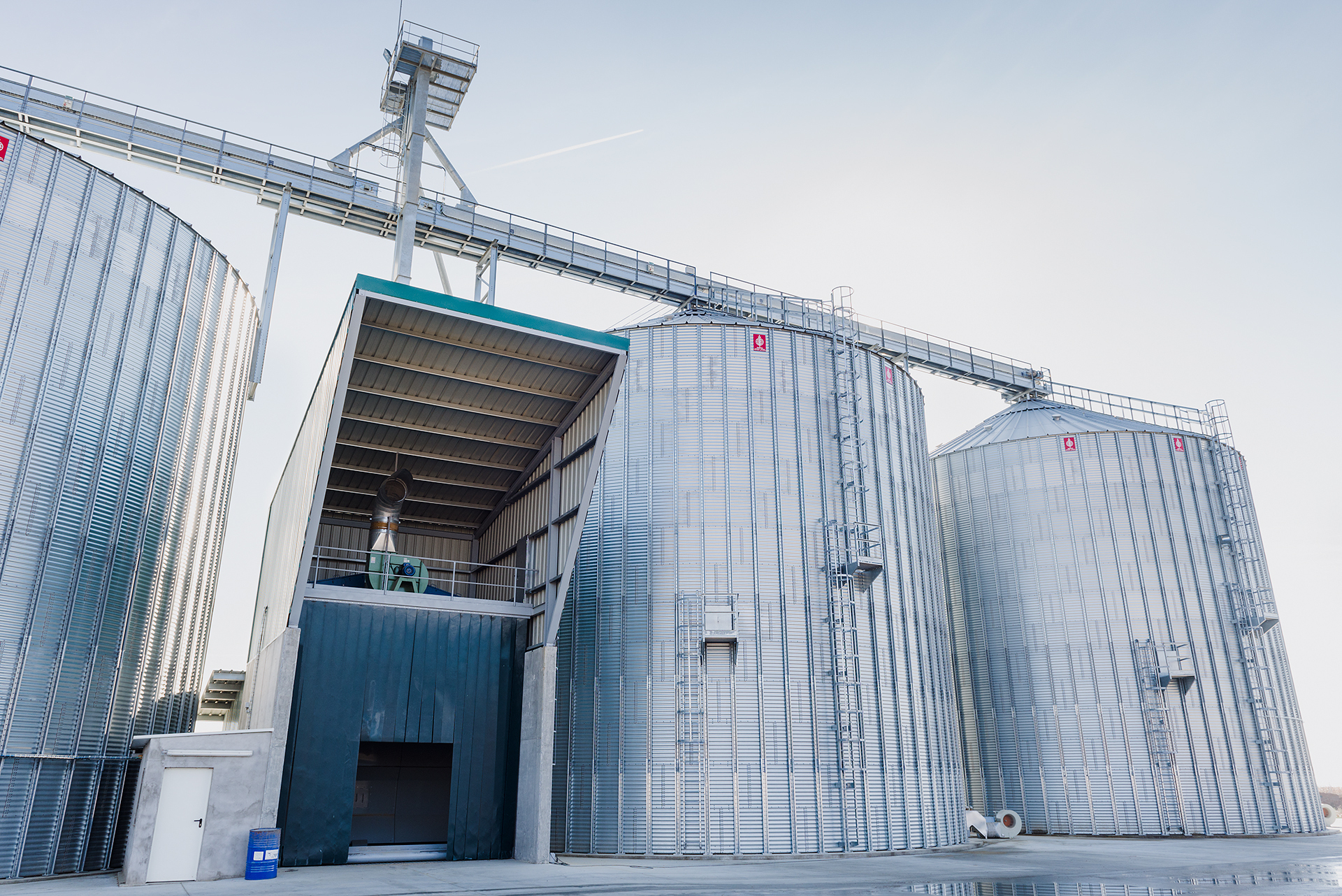
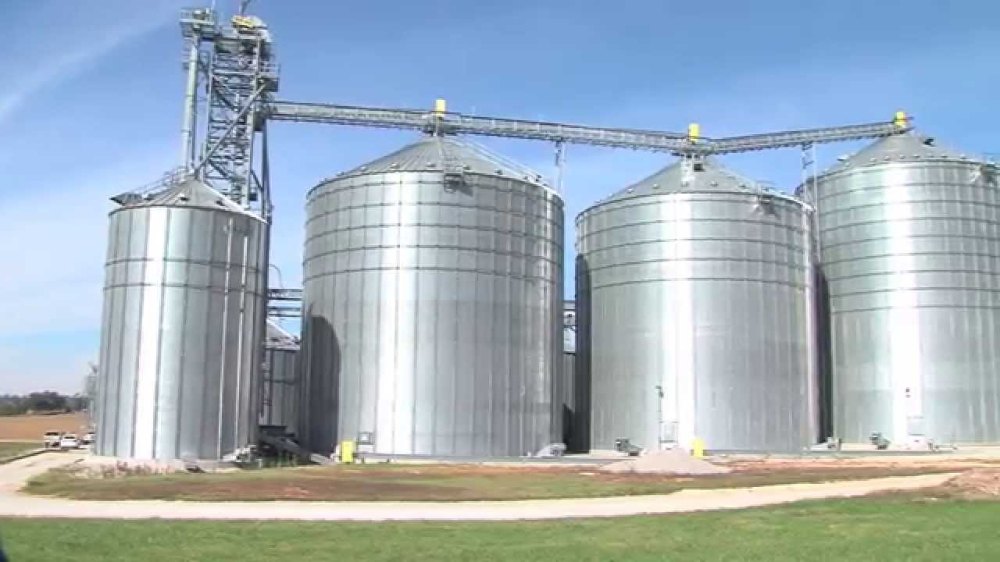
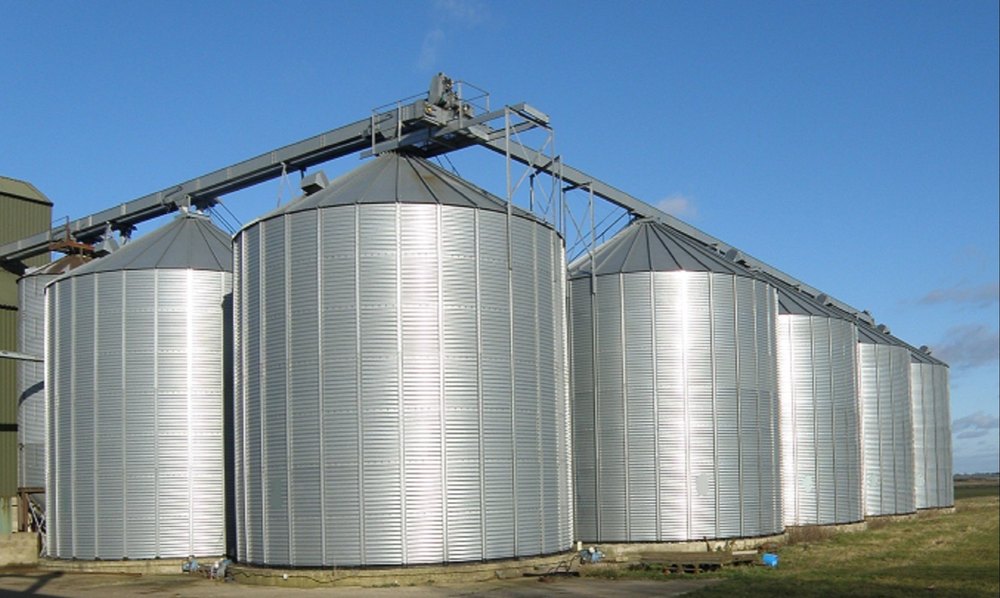
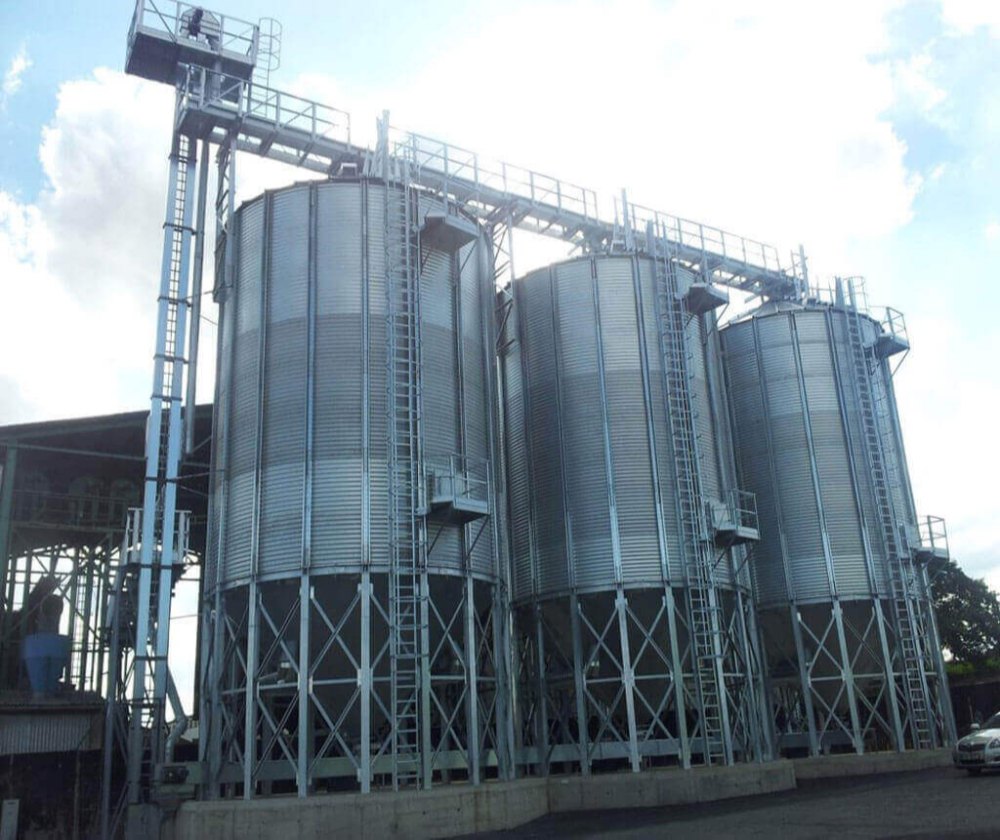
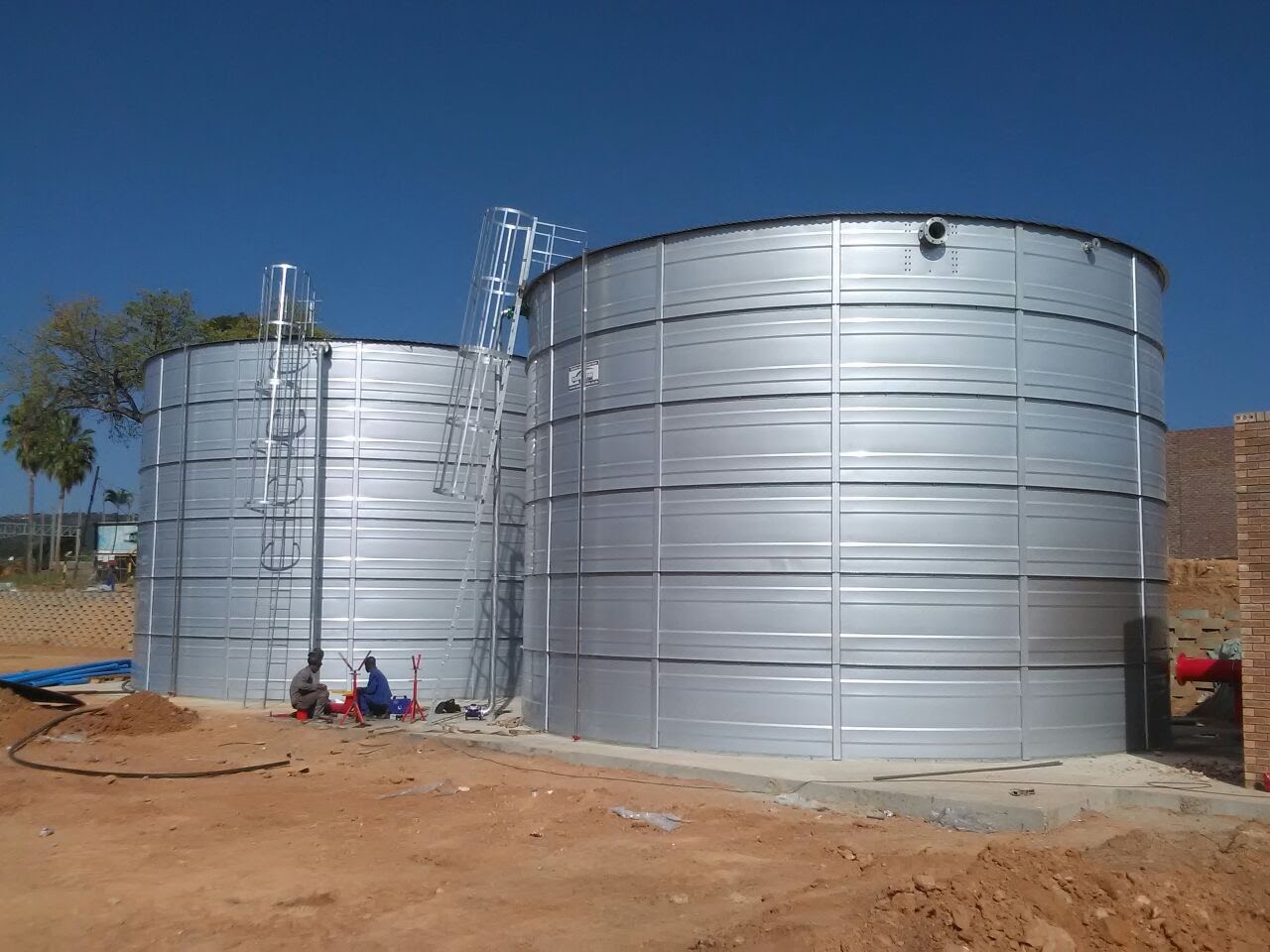
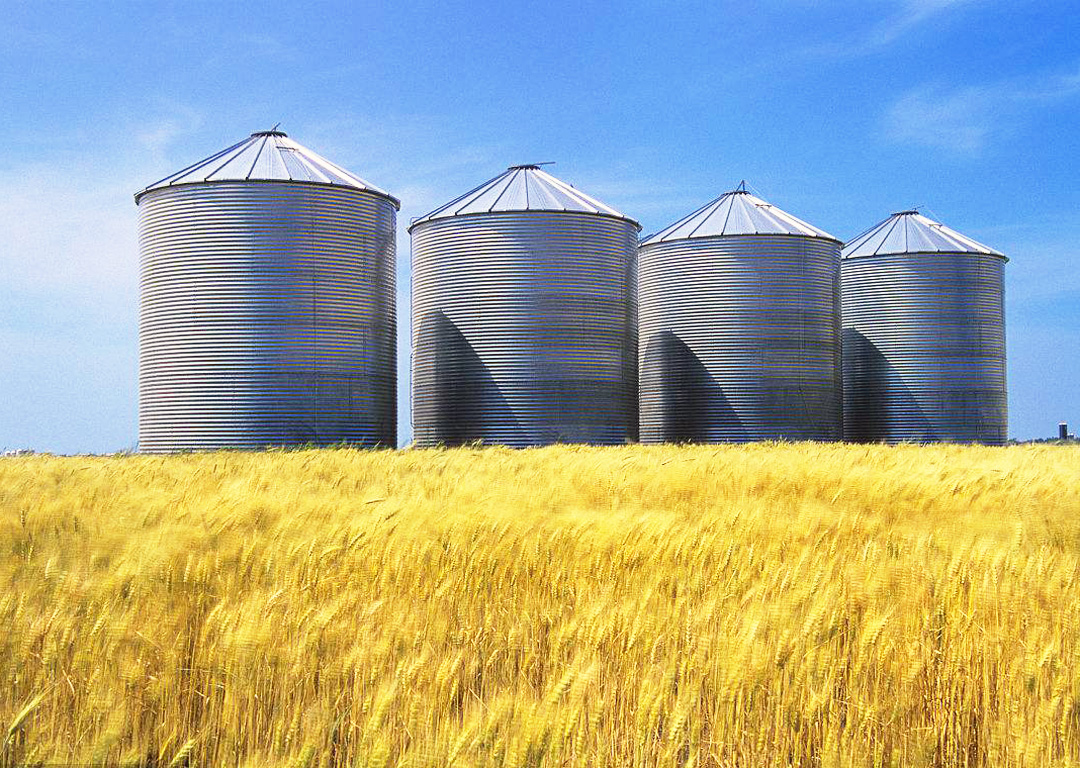
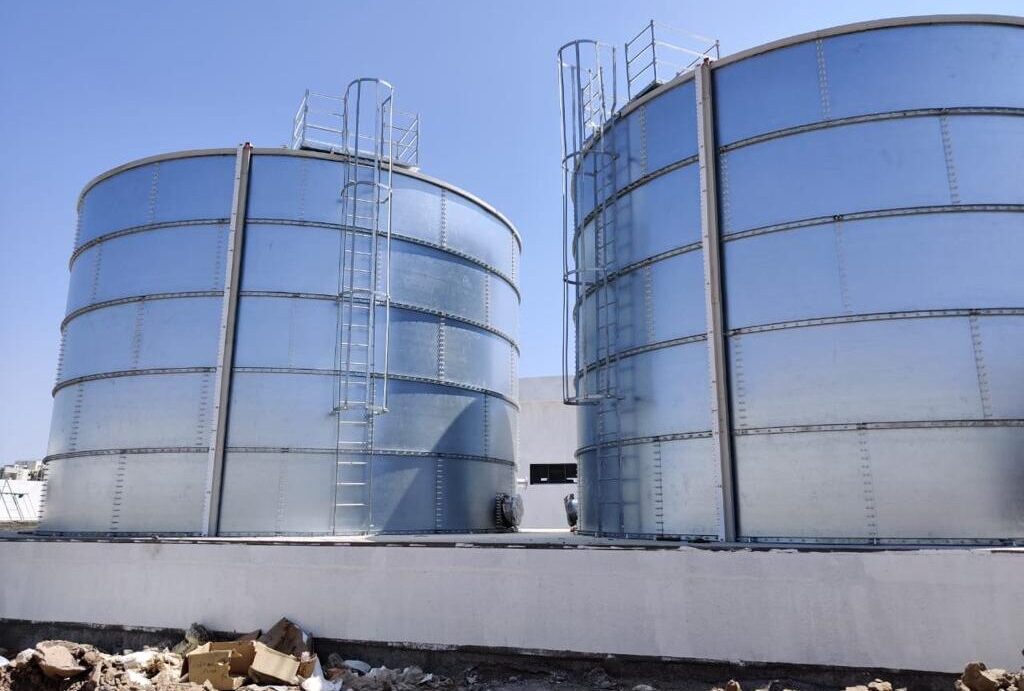
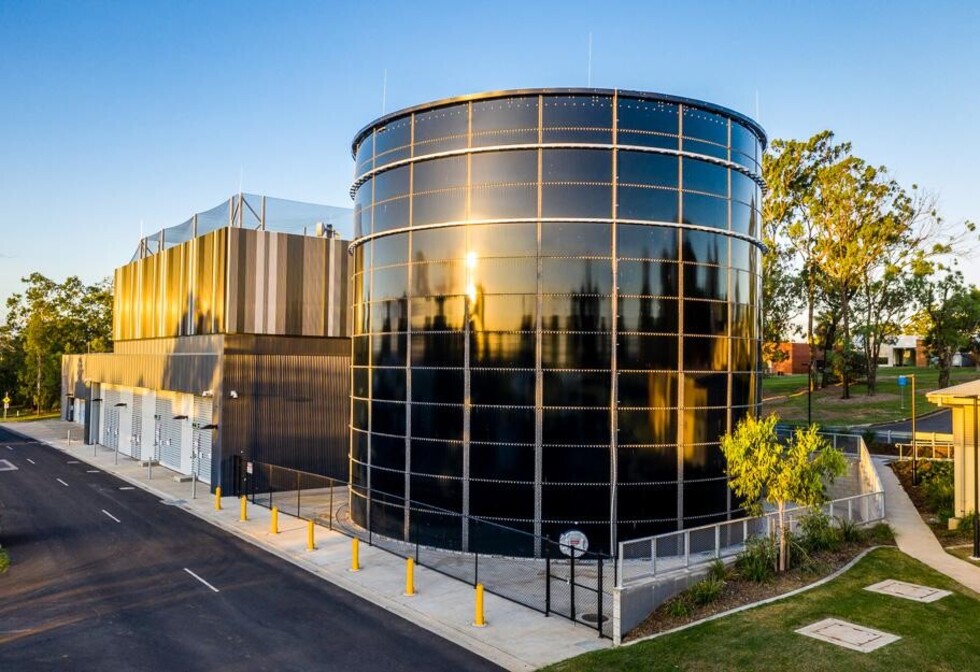
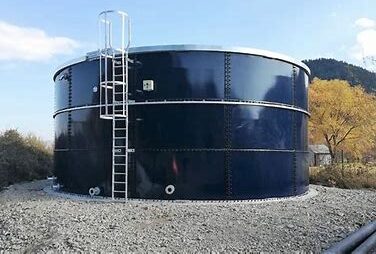
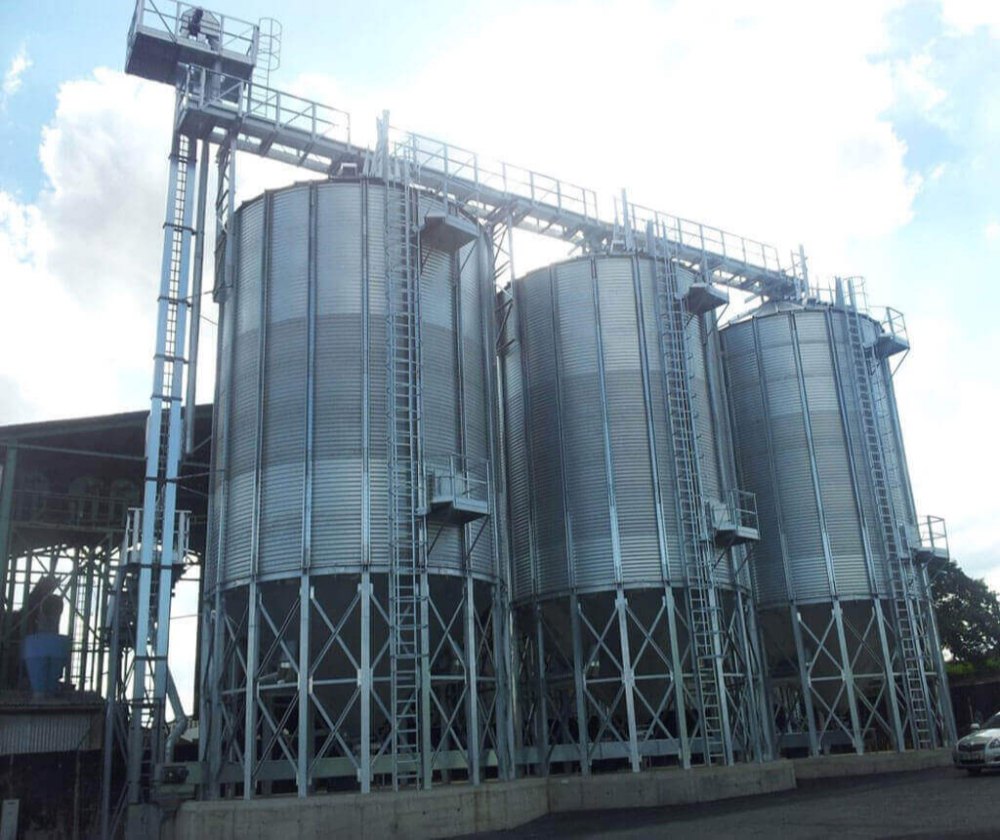